在青島某鈑金車間,張廠長正面臨多數(shù)中小制造企業(yè)的典型困境:訂單批次雜、來料擺放亂、老師傅難招又難留。一條傳統(tǒng)產(chǎn)線上,三名工人彎腰俯身反復調(diào)整零件位置,才能讓機械臂勉強抓取——直到一套搭載3D視覺引導系統(tǒng)的協(xié)作單元落地,情況徹底改變:無序堆放的工件被精準定位,機器人自適應調(diào)整軌跡,切換產(chǎn)品時工人只需在屏幕上拖拽模塊。短短三個月,這條產(chǎn)線效率提升70%,人力成本下降40%。
這正是當前中小制造企業(yè)自動化轉(zhuǎn)型的縮影:傳統(tǒng)工業(yè)視覺難以應對柔性化生產(chǎn)需求,而融合高精度3D視覺的引導技術(shù),正以低投入、快部署、強適應性破解困局。
一、四大核心場景:直擊中小企業(yè)產(chǎn)線痛點
中小企業(yè)的產(chǎn)線痛點往往高度相似——多品種混線、來料一致性差、換產(chǎn)頻繁、空間受限。3D視覺引導技術(shù)通過“手眼協(xié)同”智能,在多個場景中展現(xiàn)出變革性價值:
復雜裝配引導:告別精定位工裝
某高空作業(yè)機械廠在裝配車架時,需處理數(shù)十種金屬零件。傳統(tǒng)方案需定制高精度定位料盤(成本超20萬元且易變形),而3D視覺系統(tǒng)僅需一次拍照,即可在1.5米視野內(nèi)實現(xiàn)零件±0.3mm定位精度。即使零件帶油污、銹跡或在強環(huán)境光(>50000 lx)干擾下,仍能穩(wěn)定生成清晰點云數(shù)據(jù),裝配效率直接翻倍。
無序拆碼垛:混批生產(chǎn)不再卡殼
食品廠常需處理不同規(guī)格的紙箱混垛。通過3D視覺的點云匹配算法與預訓練模型,系統(tǒng)自動識別各類包材尺寸及抓取點,支持“混合拆垛”與“偏置抓取”。某案例中,超大視野相機覆蓋3.2×2.7米垛型,單次拍攝即完成整層定位,節(jié)省節(jié)拍30%以上。
高精度擰緊:質(zhì)量一致性破局
在裝載機車架螺栓擰緊中,人工操作易導致扭矩不均。3D視覺引導桁架機器人對螺栓中心點進行亞毫米級定位,確保擰緊槍垂直下壓。某項目一次拍照即定位單側(cè)全部螺栓,擰緊合格率從82%升至99%,同時適應數(shù)十種車架的混線生產(chǎn)。
柔性上下料:小空間發(fā)揮大價值
針對電驅(qū)殼體、變速箱鋁鑄件等復雜結(jié)構(gòu)工件,3D相機可安裝在機械臂末端(Eye-in-hand模式),配合地軌系統(tǒng)覆蓋多個料位。某汽配廠用此方案兼容了工件抓取與空托盤識別,節(jié)省地面空間40%,同時應對來料±50mm的位置偏移。
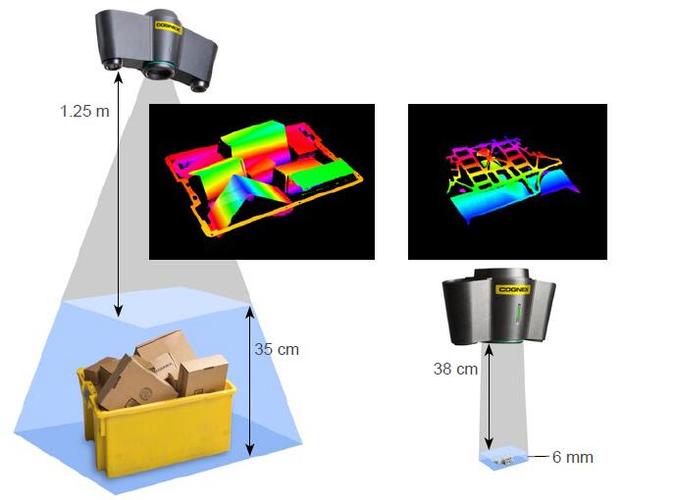
二、真實案例:中小企業(yè)低成本改造典范
案例1:10人機加工車間的“重生”
青島某家族式機加工廠承接汽車小零件訂單,原有專機無法適應新工件。改造方案:
在原有CNC旁加裝協(xié)作機器人+3D視覺單元
視覺系統(tǒng)自動識別隨意堆放的毛坯件并生成抓取路徑
支持每日切換3-5種工件,編程時間從3小時縮短至20分鐘
成效:投資回收期僅11個月,夜間實現(xiàn)“黑燈生產(chǎn)”
案例2:耐火材料廠的粉塵突圍
鎂鈣磚人工搬運效率低且粉塵危害大。部署方案:
案例3:轉(zhuǎn)型汽配廠的逆襲之路
某中小汽配廠承接新能源電池盒訂單,但人工焊接合格率僅85%。解決方案:
三、技術(shù)內(nèi)核:中小企業(yè)為何現(xiàn)在必須行動?
3D視覺引導技術(shù)能成為中小企業(yè)“用得起的智能化”,源于三大突破性進展:
精度與適應性兼得
新一代線激光振鏡相機通過多光譜融合技術(shù),攻克金屬反光、暗色吸光表面成像難題。例如在制動零部件裝箱場景中,系統(tǒng)可清晰識別高吸光黑色托盤的卡槽結(jié)構(gòu),抓取成功率>99.5%。
快速部署落地
圖形化軟件平臺(如RobotPilot)支持拖拽式流程搭建,無需專業(yè)編程。某家具廠工人經(jīng)2天培訓即能自主配置新工件模板,適配周期從周級壓縮至小時級。
投資回報可測算
模塊化方案(3D相機+標準機器人+通用軟件)將投入門檻降至15-30萬元。多數(shù)案例顯示,8-12個月即可收回成本,遠低于傳統(tǒng)自動化方案。

特別提示:青島及山東多地政府對“智改數(shù)轉(zhuǎn)”提供30%-50%補貼,部分園區(qū)開放綠色審批通道。一套滿足中小產(chǎn)線需求的3D視覺引導系統(tǒng),實際投入可低于一輛商用貨車。
當隔壁工廠開始用3D視覺“看清”世界時,您的產(chǎn)線是否還在盲人摸象? 工業(yè)3D視覺引導技術(shù)已不再是巨頭的專屬玩具。它如同為機器人裝上自適應之眼,讓中小企業(yè)的產(chǎn)線真正具備柔性進化能力——無論是工件隨意堆放、還是訂單頻繁切換,系統(tǒng)總能實時感知、動態(tài)決策。
我們?yōu)榍鄭u地區(qū)企業(yè)提供零門檻產(chǎn)線診斷:只需拍攝一段現(xiàn)場視頻,48小時內(nèi)即可獲取《3D視覺適配性評估報告》與《ROI測算方案》。讓您的自動化改造不再“盲選”,而是基于數(shù)據(jù)的精準升級。
3D視覺引導協(xié)作機器人無序抓。褐行∑髽I(yè)智能制造升級的革新方案