在工業(yè)自動化浪潮中,中小企業(yè)常面臨兩難困境:高端3D視覺方案成本高昂、實施復雜,而傳統(tǒng)人工操作又存在效率瓶頸與品控波動。2D視覺引導技術憑借其成熟穩(wěn)定的性能、更低的部署成本與卓越的適應性,成為中小型企業(yè)邁向智能制造的“第一塊跳板”。它讓機器人真正擁有了“眼睛”和“大腦”,在精度與效率之間找到了黃金平衡點。
一、技術基石:2D視覺如何為機器人賦予“精準視線”
2D視覺引導技術的核心在于通過工業(yè)相機捕捉目標物體的平面圖像信息,結合高速圖像處理算法,實時識別物體的位置、角度及關鍵特征點,并將坐標數(shù)據(jù)同步傳輸至機器人控制系統(tǒng)。這種技術突破傳統(tǒng)點位示教的局限,實現(xiàn)三大能力飛躍:
動態(tài)定位補償:適應來料位置偏差,消除人工上料誤差;
多姿態(tài)識別:通過特征匹配精準判斷物體角度,引導機器人精準抓取或裝配;
強抗干擾能力:結合專用光源與濾波算法,可應對油污、反光、遮擋等復雜工況。
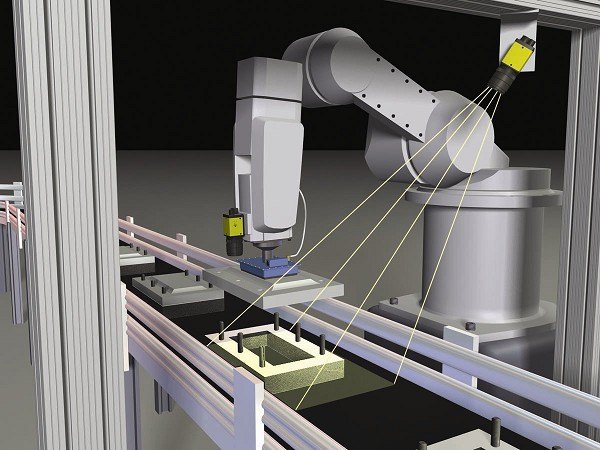
案例啟示:汽車卡簧全自動裝配難題破解
某汽車配件廠在座椅電機組裝中,需將表面沾滿油脂的卡簧精準裝入槽位。傳統(tǒng)人工放置因視覺疲勞導致錯誤率高達5%。部署2D視覺系統(tǒng)后,通過2000萬像素高清相機+環(huán)形抗眩光光源組合,實時計算卡簧角度與中心偏移量,引導機械手完成0.1mm精度對位。系統(tǒng)實現(xiàn)“一拖二”同步檢測雙工位,錯誤率降至0.02%,節(jié)省質檢人力3人/線。
二、場景突破:2D視覺在關鍵工藝中的增效實踐
(1)去毛刺工藝:告別人工銼刀時代
鑄件、注塑件毛刺去除是機加車間的典型痛點。某中小五金廠采用2D視覺引導機器人系統(tǒng):
精準定位:相機掃描工件表面,識別毛刺區(qū)域坐標與高度范圍;
自適配路徑:機器人根據(jù)視覺數(shù)據(jù)動態(tài)規(guī)劃打磨力度與軌跡;
多品種混線:系統(tǒng)可記憶上百種工件模板,切換生產時無需重新編程。
成效:去毛刺效率提升200%,產品表面不良率從8%降至0.5%,年節(jié)省返工成本超50萬元。
(2)料框拆垛:小空間里的大作為
針對汽車零部件廠商的物料周轉需求,集成測距功能的2D視覺方案實現(xiàn)突破:
空間感知升級:通過激光測距模塊(150-2500mm范圍) 同步反饋工件深度信息;
防碰撞路徑:機器人依據(jù)距離數(shù)據(jù)動態(tài)調整抓取軌跡,縮短空行程時間;
緊湊型設計:相機直接集成于機器人夾具,無額外工控機占用空間。
成效:拆垛節(jié)拍時間縮短35%,在金屬件反光工況下仍保持99.8%抓取成功率。
三、為什么中小企業(yè)更應關注2D視覺?(投入產出比實測)
相比3D視覺動輒數(shù)十萬的硬件成本,2D視覺系統(tǒng)具有顯著優(yōu)勢:
維度 | 2D視覺方案 | 傳統(tǒng)人工/固定工裝
|
初始投入 | 5-15萬元(含相機+軟件+集成) | 3D視覺方案約3-5倍成本6 |
部署周期 | 1-3周(標定簡單) | 3D系統(tǒng)需復雜點云標定 |
柔性能力 | 支持產品換型≤10分鐘 | 需重新設計夾具/程序 |
維護難度 | 模塊化更換,技術支持廣泛 | 依賴專業(yè)算法團隊調試 |
某電子連接器企業(yè)實證:
在插針檢測工位部署2D視覺定位系統(tǒng)后,設備投資回收期僅5.2個月。通過降低漏檢率避免的客戶索賠,年間接挽回損失超80萬元。
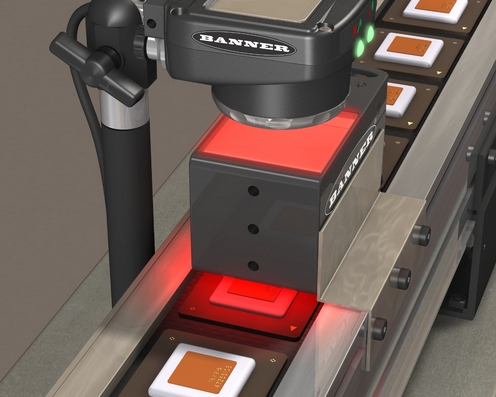
四、未來兼容:2D視覺的智能化演進路徑
隨著AI算法融合與多傳感器協(xié)同技術的發(fā)展,2D視覺系統(tǒng)正突破傳統(tǒng)局限:
深度學習加持:實現(xiàn)復雜背景下的特征提取,適應工件紋理變化;
2D+測距模塊:以低成本實現(xiàn)準三維定位,滿足堆疊件分揀需求4;
數(shù)據(jù)集成延伸:視覺數(shù)據(jù)與MES/PLC系統(tǒng)直連,構建生產追溯閉環(huán)(如壓裝曲線綁定二維碼)。
專家視角:
“未來五年內,2D視覺仍將占據(jù)工業(yè)應用超70%份額。其核心價值在于用極簡架構解決絕大多數(shù)平面引導需求,是中小企業(yè)智能化改造的最優(yōu)解!薄I(yè)視覺技術白皮書2025
結語:低成本、快部署、高可靠
對于預算有限卻亟需提升良率、減少人力依賴的中小制造企業(yè),2D視覺引導技術不是過渡方案,而是經全球驗證的成熟選擇。它用可預測的投入撬動生產效率躍遷,讓“機器替人”不再是大企業(yè)的專屬特權。
無論您身處汽配、五金、電子或家電行業(yè),如果面臨定位不準、檢測低效、換線繁瑣的痛點,2D視覺引導方案都已準備好,成為您車間里那雙永不懈怠的“智能之眼”。